Quality Is a Process, Not a Result
Quality Management Systems (QMS) start at the beginning of production processes with digitalised and connected data collection. Based on quality data it’s simple to automate processes, create root-cause analysis and improve the processes.
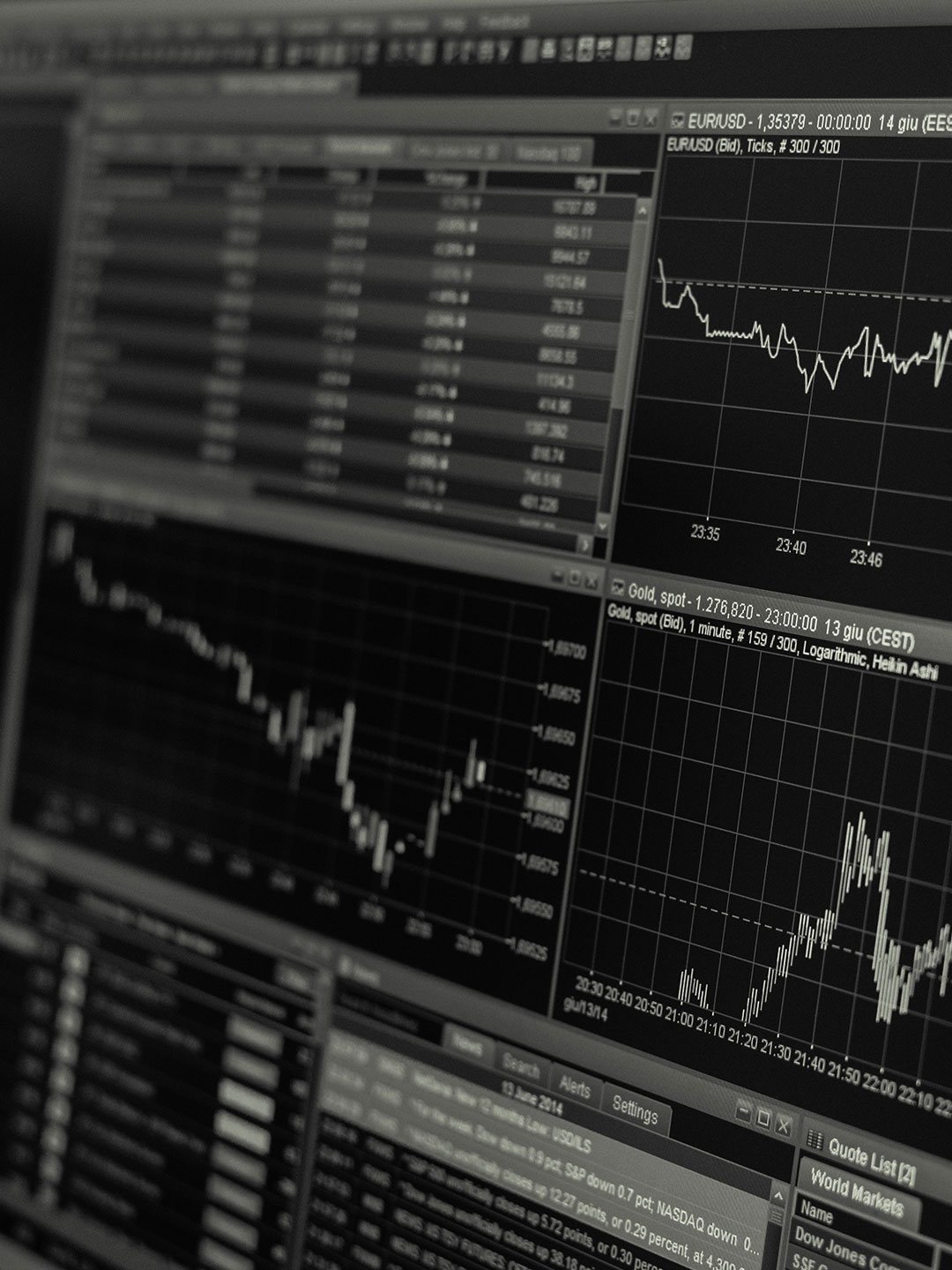
Understand What Is Happening, When Its Happening
As the Quality Control processes in manufacturing evolve, there’s a trend toward more inline metrology, or even toward process integrated measuring instruments, minimising control loops. Measurements should no longer be taken in a separate room or area, but directly on the production line. Metrology should be applied in a modularised mode in factories and production lines, that allows to reduce the use of standard measuring instruments.
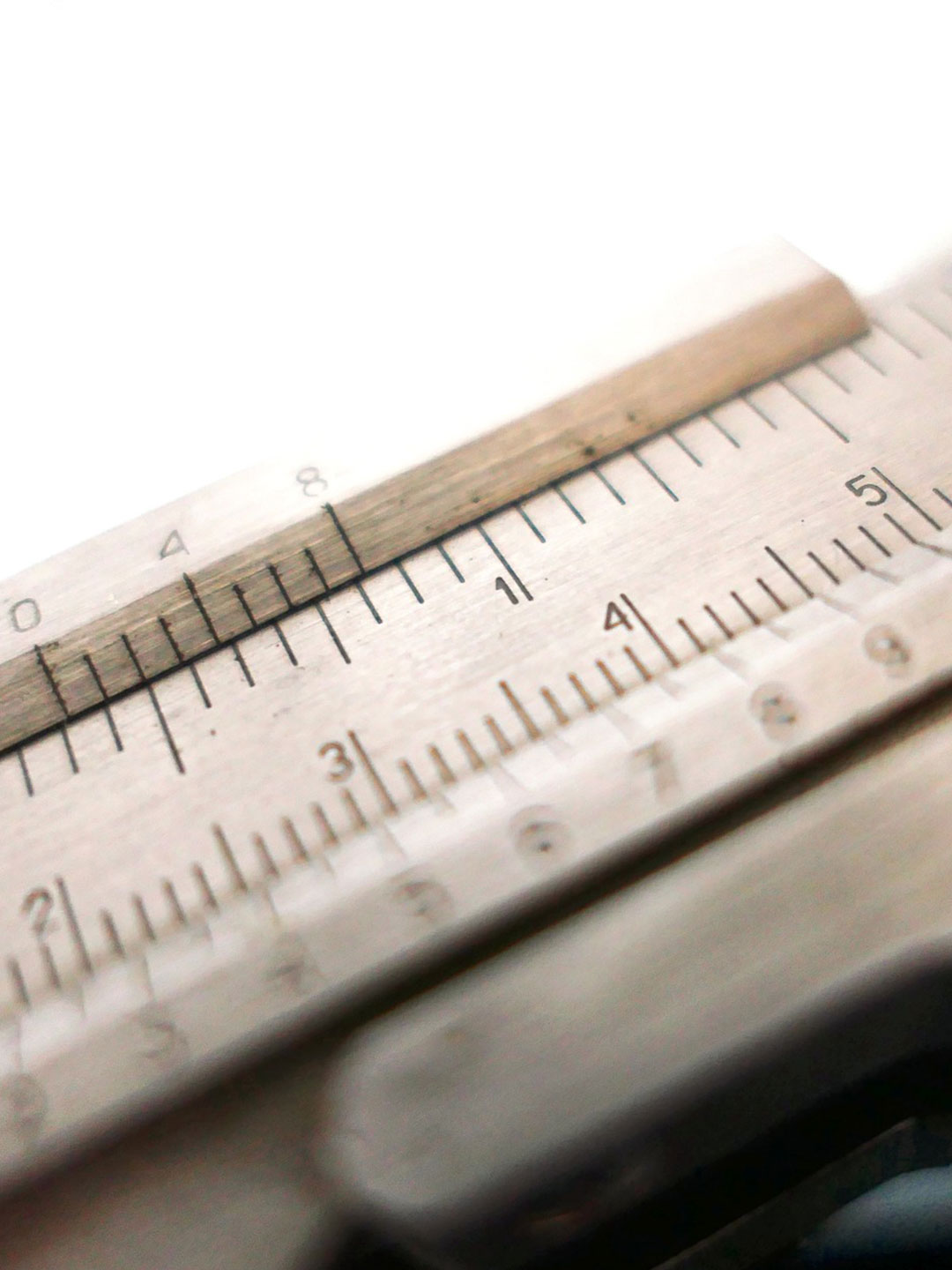
Self-Learning is Self-Healing
A more optimised quality assurance process could lead to a better-quality product with fewer defects. The self-optimisation is a characteristic of the smart factory, that can predict and detect quality defect trends sooner and also help to identify discrete human, machine or environmental causes of poor quality. That could lead to lower scrap rates and lead times while increasing efficiency and yield.
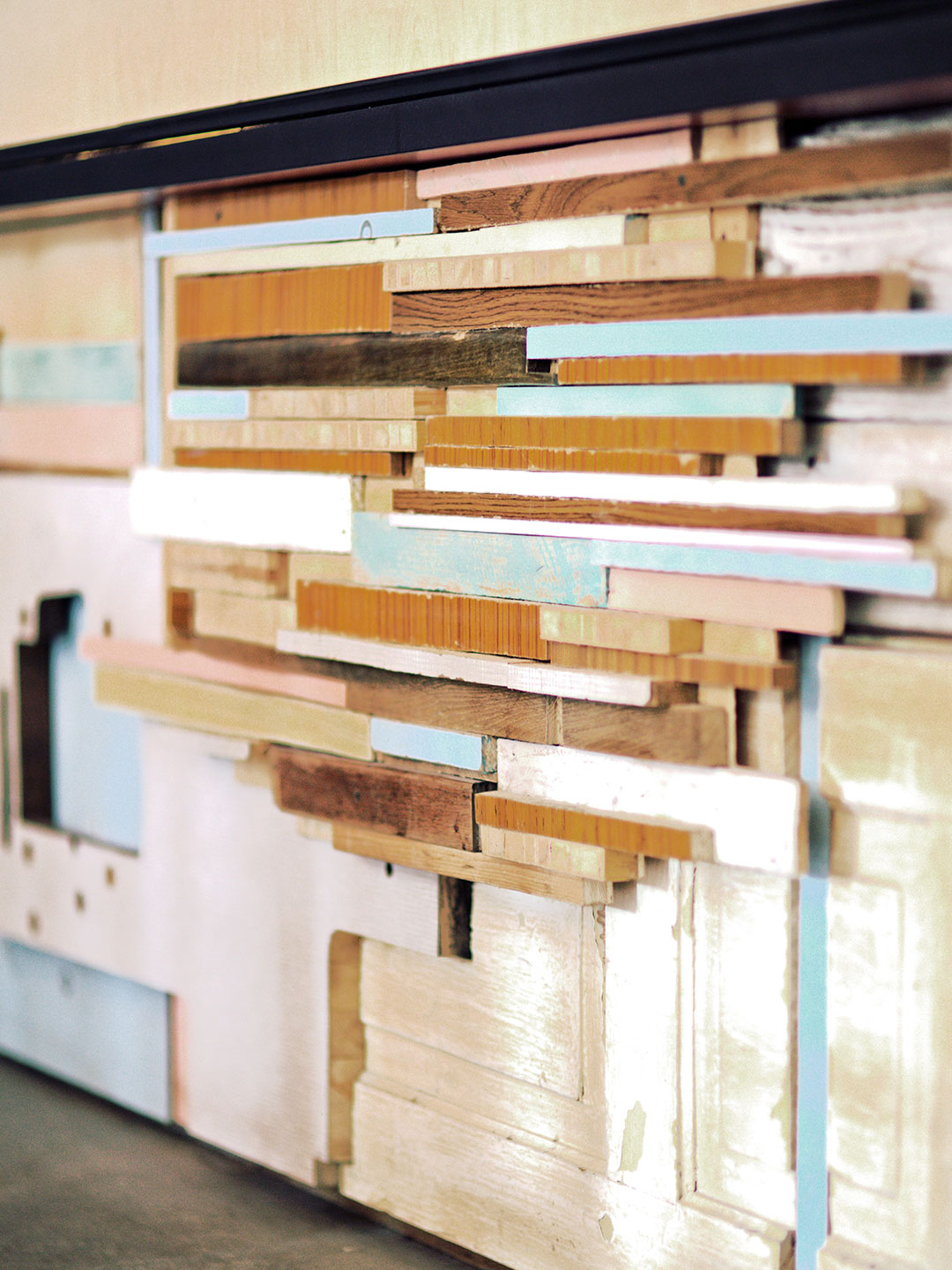