June 18, 2019
Supply Chain Professionals know the difficulties of locating their results on P&L statement under business benefits. Typical priorities in Supply Chain are: ensuring availability of materials and serving all internal customers, such as production.
Supply Chain Mission Statement after the facade is removed
“We need to buy requested items, make sure these are available when needed and not exceed the purchasing budget when doing this!”
I have often heard the following phrase from CEOs:
That is a great piece of work you have done, but what does it mean for the bottom line?
Supply Chain (SCM) function is mostly seen as a cost function and it is not a surprise to anyone that almost half of the manufacturing companies’ revenue is spent by Supply Chain.
Cost most commonly named as cost of goods sold (COGS) is linked with the income statement. For SCM it is very unfortunate that it shows up as red not green numbers and therefore it never gets same attention as sales revenue.
However, indirectly many Supply Chain Actions do impact revenue. Some examples below:
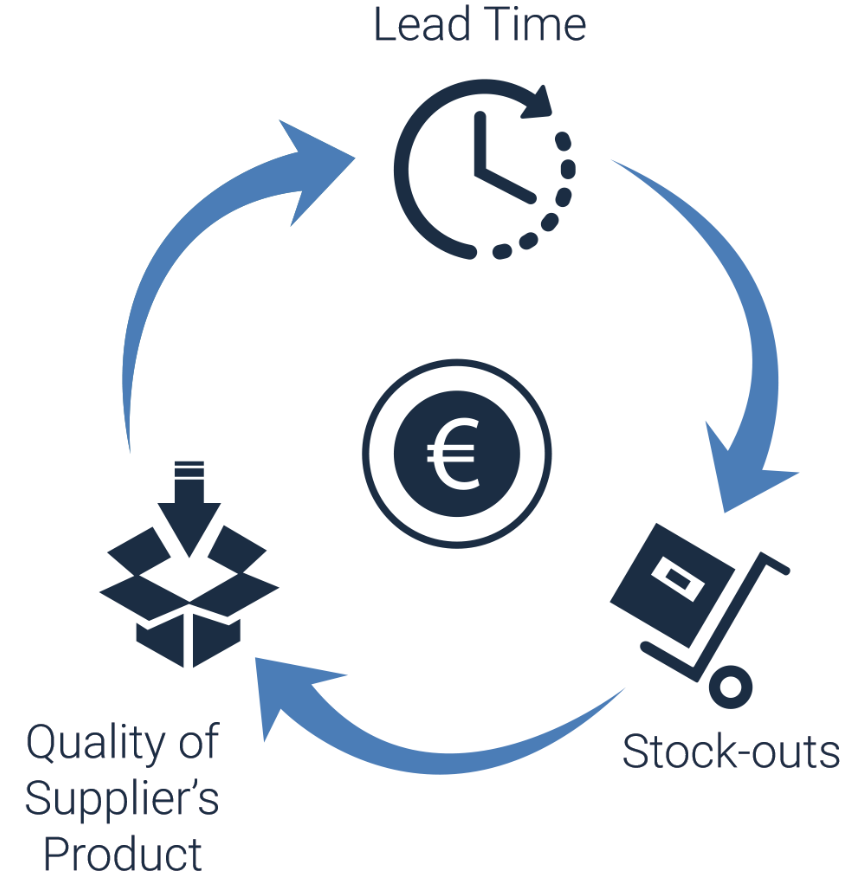
Lead Time — reducing suppliers lead-time can increase revenue
Quality of Supplier’s Product — avoiding quality problems allows to deliver what has been promised and therefore increase revenue, opposite situation can lead to revenue reduction
Stock-outs — can reduce revenue since we might not be able to finalise all planned actions.
By looking only at the Income Statement we unfortunately only end up with some hypothetical calculations and best guess estimates on how SCM affects the bottom line.
Let us now move from the Income Statement to the balance sheet, which consists of assets, liabilities and equity. From the Balance sheet components we can calculate following parameters:

Both of these parameters are directly influenced by actions performed in Supply Chain. One of the goals for everyone working in supply chain should be to understand Working Capital components and the cause / effect paradigm.
Without drilling down to details we might say that high working capital ratio is good, but since liabilities include inventories, (beside accounts receivables and cash) it can also be that we have excessive amount of inventory in our books, which is not necessarily good.
Inventories are not only linked with Supply Chain but also with sales and manufacturing. Therefore Supply Chain itself cannot solely reduce inventories although inventory reduction plan can be something where Supply Chain should take the lead role.
In order to see benefits from Inventory Reduction Programs, then best option would be to follow and increase the ITO (Inventory Turnover) rate. Higher rate is always better and trend should be like climbing on top of the hill. Different industries have different standards and benchmarking against these standards can be very valuable practice.

Current Liabilities include accounts payables (beside taxes, salaries to others)or in other words outstanding invoices we need to pay to our suppliers. Supply Chain can influence suppliers and renegotiate items’ cost. However, a calculation of how much one negotiation affects the whole working capital or working capital ratio is often difficult and redundant.
When coming back to the initial question from the CEO regarding the bottom line then by only looking at the balance sheet it is very difficult to point to an exact number and say that this is the one showing Supply Chain’s contribution.
Next we look into CCC (cash conversion cycle) components, which show how many days it takes to convert cash from companies investment into working capital. A shorter cycle indicates a healthy, more liquid company.
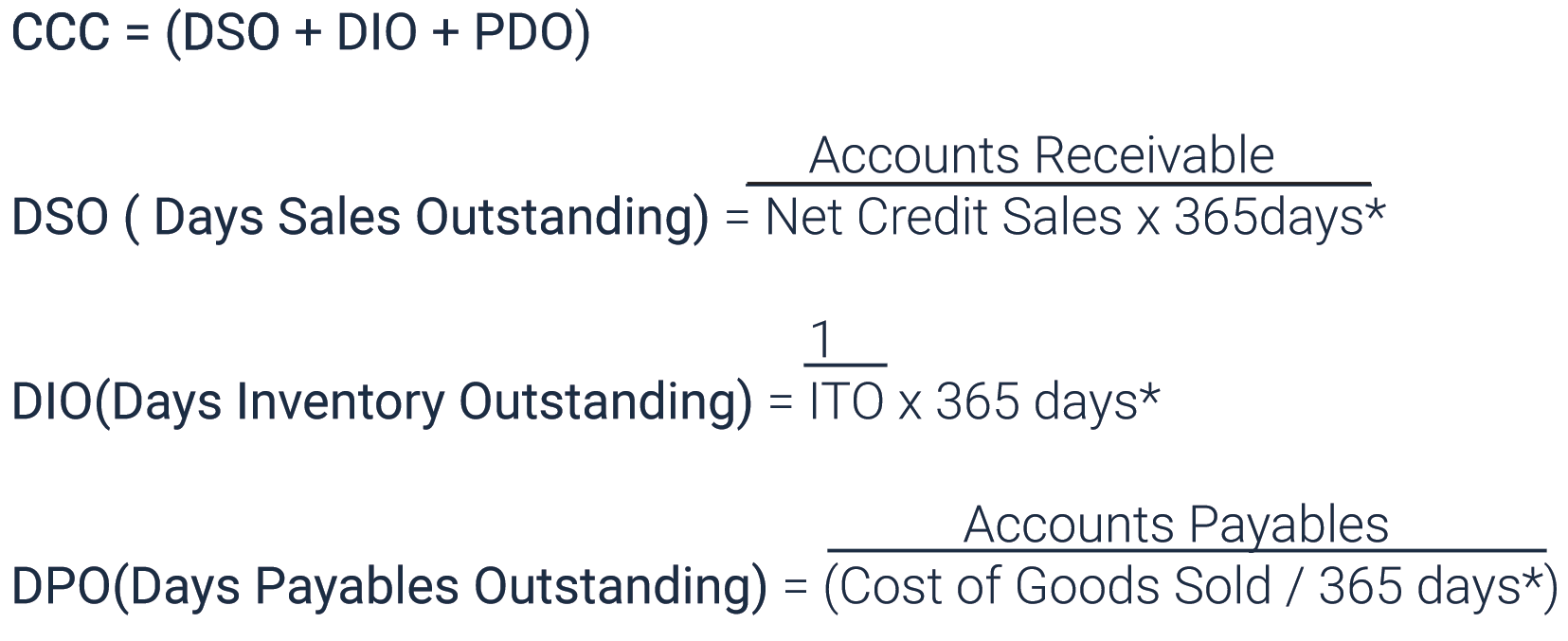
Both DPO (days payables outstanding) and DIO (days inventory outstanding) can be linked directly with Supply Chain. Increasing supplier payment terms will lead to increased numbers or days payables outstanding (DPO), which will decrease CCC.
By knowing all the above and being a true Supply Chain professional we can provide the CEO following response to initial question:
Dear CEO,
Thank you for your question and recognition for the work we have done in Supply Chain. I have given some thought to the bottom line question and in fact there are components from Supply Chain seen in both the profit and loss statement and in the balance sheet. However, it is difficult to draw direct conclusions from our actions looking at these financial statements. Supply Chain is just one of the functions in our company and end results are mixture from sales, production, supply chain, R&D and others. I would recommend implementing KPIs such as ITO, CCC and start monitoring our Average Payment Term of our suppliers.
VP in Supply Chain.
Considering everything written above we must remember that Supply Chain is a highly data driven function, therefore decision making is supported by data quality and interpretation.
Tarmo Saidla is a Head of Supply Chain Excellence in Neurisium. He is responsible for Supply Chain Business Strategy and helps Customers to implement Industry 4.0 standards across the whole Value Chain. He uses both Supply Chain Expertise and Data Analytics skills to provide real value for Customers.