June 10, 2020
The Pandemic has swept across the world and upended the way that almost every industry operates, including the manufacturing industry. Going forward, businesses may need to rethink their strategies and implement drastic changes.
For engineers, these changes may include adopting more smart manufacturing solutions for increased automation and less reliance on physical labor. COVID-19 may bring the end of on-site monitoring and greater reliance on artificial intelligence.
The Pandemic Is Accelerating Automation in Manufacturing
Factory automation is not a new concept. In recent years, a growing number of engineers have implemented optimised production technology featuring machine learning and IoT to streamline production lines. However, the pandemic is forcing many companies to accelerate these efforts.
Artificial intelligence (AI), machine learning, and automation are not buzzwords. They are the latest solutions for improving existing principles.
Many engineers will agree that the introduction of the assembly line by Henry Ford was one of the first examples of factory automation. The assembly line is still a predominant component of manufacturing today but modern technology is revolutionising the process.
Using Smart Manufacturing for Improved Quality Control
The latest quality control tools aim to reduce the need for on-site monitoring using physical labor. Traditionally, production lines include multiple quality control checkpoints. Employees or supervisors look for defects before a component moves on to the next stage of the production line.
Computers have been part of this process for many years. Computers are commonly used to ensure that components are the right shape or weight while humans are considered better at identifying cracks and colors. However, the technology is starting to outpace human capabilities.
Smart manufacturing involves the use of sensors to monitor every stage of the production process. The sensors relay information to a central database, which evaluates the results to detect defects and quality control issues. These systems have become much more skilled at identifying defects.
When combined with machine learning, smart production technology may be able to improve the detection of defects by up to 90%.
Relying on Machine Learning for Predictive Maintenance
Quality control is not the only reason why production lines require real-time monitoring. Engineers also need to ensure that the machines keep running. Many manufacturers rely on a semi-manual approach to predictive maintenance. They use advanced systems, such as SCADA systems, to alert engineers to maintenance issues.
With the semi-manual method, thresholds and alerts are configured by humans. As with any human-operated task, there is a risk for errors. A static set of rules may not account for certain variables, which can lead to false alerts.
Machine learning can improve predictive maintenance by eliminating human error and accounting for a greater range of variables. Complex algorithms are used to process big data.
The data comes from sensors connected to the machines on the production line along with historical data related to production flow and other metrics. The algorithms help detect patterns and anomalies to provide greater accuracy.
Factory automation becomes less efficient if the machines stop working. By implementing machine learning, engineers can detect issues before malfunctions occur.
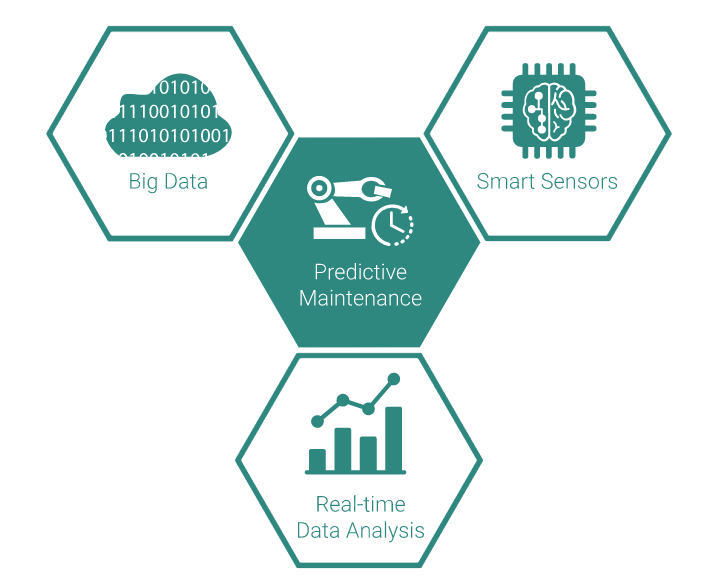
Machine Learning Enhances Logistics and Inventory Management
Logistics and inventory management are essential to the production process. Without raw materials, the production line comes to a halt. This is another area where machine learning is helping to increase efficiency and reduce waste.
By analyzing big data obtained from the production floor, inventory warehouse, vendors, and the rest of the supply chain, AI software can help coordinate the logistics of your inventory.
McKinsey estimates that by 2030, most repetitive and data related supply chain and logistics operations could be automated by AI . Allowing machines to handle these tasks saves time and money while ensuring that you have the materials needed for production.
Having too much of a specific material may result in waste. A lack of specific materials may slow the production process. Machine learning keeps the production lines moving by providing greater efficiency for inventory management, resulting in less waste and fewer stoppages.
Factory Automation Technology Eliminates Manual Labor
Automation already reduces the need for manual labor on the production floor. Machines can perform the most physically demanding jobs on the production line. In some cases, human workers are mostly comprised of engineers and technicians who monitor the machinery.
If machine learning can eliminate the need for on-site monitoring, production floors can become entirely automated. Data from the production line is fed to a machine that monitors every aspect of the production process from predicting maintenance needs to detecting defects. When an issue arises, the software triggers an alert, which an engineer can then review and resolve.
As the data is supplied to a computer, it can be transmitted anywhere. With an increasing dependence on cloud-based solutions for big data and artificial intelligence (AI), engineers do not need to be physically present to monitor the production line.
Creating a Safer Work Environment Using the Latest Technology
The coronavirus pandemic has already forced thousands of manufacturers to temporarily shut their doors. The risk of workers spreading the virus is too great. There have also been outbreaks at major manufacturing facilities. This has left companies scrambling for a way to resume production.
Reducing the number of workers on the floor may provide a path forward. The latest technologies offer additional automation. Without the need for manual on-site monitoring, it becomes easier for companies to create a safer work environment.
Factory automation has already reduced the need for manual labor and machine learning is poised to reduce the need for on-site monitoring. Depending on the scale and scope of the production line, a company may only require a handful of engineers and technicians on site. In the coming years, it may be possible to eliminate the presence of humans altogether.
While some companies are hesitant to embrace machine learning and AI, they risk getting left behind as other companies adapt to the new normal. Using these technologies may be necessary for complying with local regulations related to the maximum number of workers in a facility or social distancing requirements.
When the pandemic finally passes, the companies that implemented the latest technologies will be better positioned to lead their industries into the next stage of manufacturing.