April 6, 2021
Manufacturing is going through the fourth industrial revolution as many are using large-scale data analysis, artificial intelligence, machine learning, and the Internet of things (IoT) to dramatically improve efficiency. The following information explores the impact of these initiatives on the manufacturing industry and the business processes that often have not changed for decades.
Big data and data analytics
With increasing complexity of Industry 4.0, data-based decision making has become the new norm in manufacturing. Traditionally it has been sufficient to rely on engineer's knowledge and maintaining buffers to handle fluctuations in production. However, the move towards smaller batch production demands smaller buffers and the complexity of manufacturing lines combined with constant changes in settings is becoming a greater problem for the engineer to overcome.
Luckily, data analysis is stepping in to allow us to dive into production data generated by operational technology. Big Data makes is possible, for example, to start predicting changes in physical systems for maintenance, find bottlenecks in production lines and detect sources of quality issues.
Machine learning and artificial intelligence
The rise of big data and the lowering cost of computation has opened the path for the rapid increase of machine learning applied in manufacturing. As a next step from analytics, these intelligent systems are able to look at data as well as make decisions on it.
As the field is still growing, we are currently seeing mostly single focus intelligent systems - narrow AI, that helps us with individual defined tasks. For example, AI powered systems that BMW is using for automated quality control. However, the future will be looking towards fully automated production factories as well as human-robot collaboration.
Capgemini Research Institute has carried out an insightful research into AI in manufacturing operations, exploring several use cases in different manufacturing settings.
Advanced robotics
Advanced robotics combines sophisticated programming and powerful hardware that make use of smart sensor technology. Advanced robotics can be used in manufacturing facilities that run around the clock, without human oversight. Industry 4.0 with advanced robotics is making a huge impact on manufacturing as the processes increase in complexity and scope thanks to digitalisation and the application of advanced computing technologies (AI and ML).
The new more complicated operating environment demands an increasing amount of automation. Additionally, use of advanced robots offers advantages over conventional robots in that they are easier to set up and configure on an assembly line. They are also able to use simulation software to learn how to perform an array of tasks. This is a very desirable attribute for companies that use production systems which require many adjustments during the course of production.
Industry 4.0 uses advanced robotics to increase productivity by taking over manual tasks and accomplishing them faster. One example is the assembly of flexible parts – advanced robots can utilise their ability to adjust themselves and course correct when procedures or processes change on the assembly line. Conventional robots have to be stopped for reconfiguration in such situations.
Due to ongoing pandemic of COVID-19, some production lines have been converted to manufacturing the PPE and other medical equipment. The Mercedes F1 team repurposed their production line of pistons and turbochargers to making of the ContinuousPositive Airway Pressure (CPAP) devices. It took them less than 100 hours from the initial meeting to production of the first device.
Simulation
Digital twin technology is becoming more widespread, as the proliferation of IoT technology accelerates the growth. In manufacturing there are 4 main digital twin applications – product development, design customisation, shop floor performance improvement and predictive maintenance. Ultimately, a greater insight into the plant’s operations supports better and faster decision-making throughout the entire organisation, enabling to reduce equipment downtime and optimise production processes.
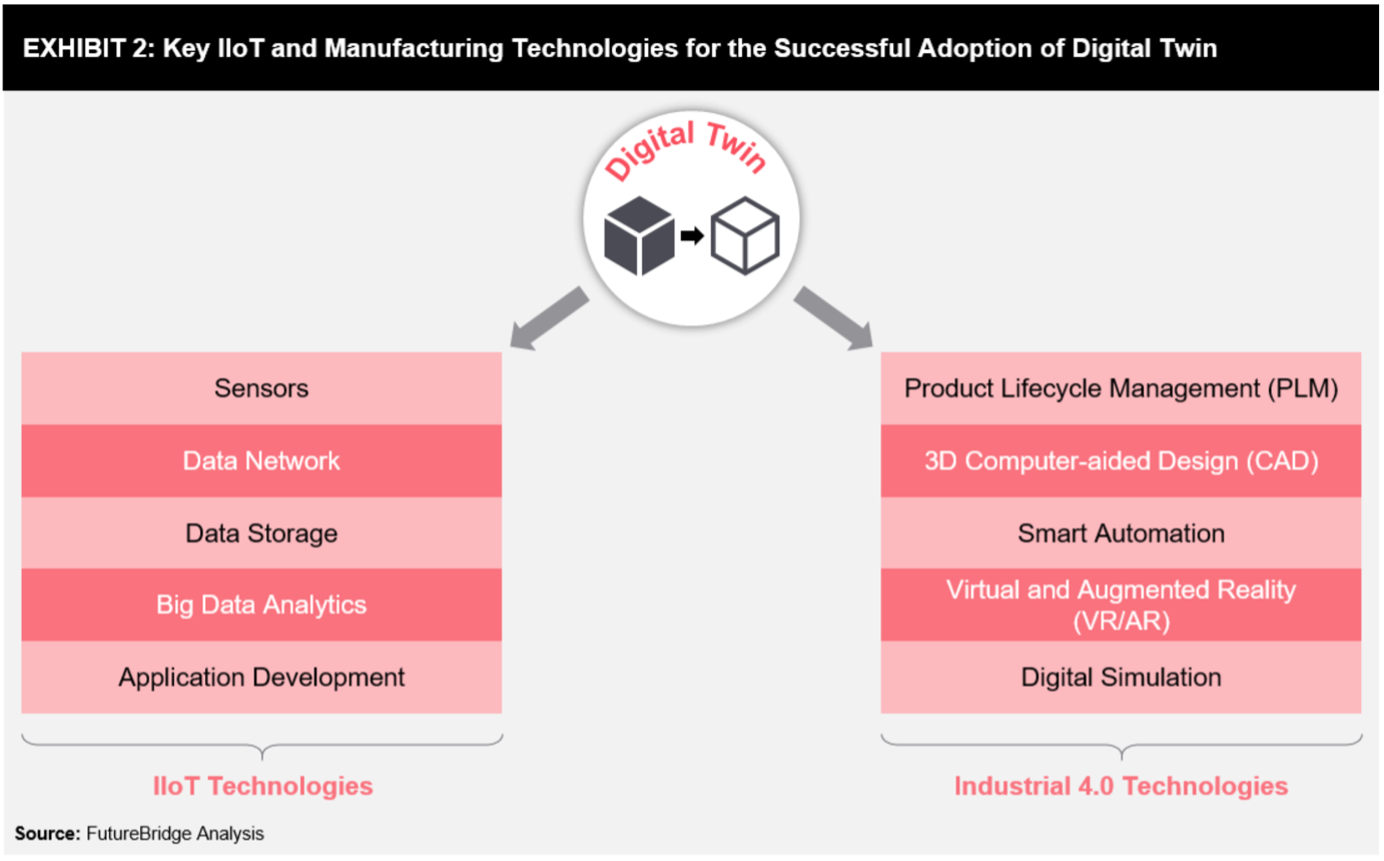
In recent years, Maserati and Siemens have cooperated on creating digital twins of their car models and production processes. Their initial application was the optimisation of car aerodynamics. As running of the wind tunnel is expensive, Maserati was looking to utilise digital technology to reduce the design and development cost of its vehicles. Due to the need to introduce new models to the market at ever-decreasing intervals and control more and more complex network of suppliers, they have utilised digital twin technology throughout their development processes. Simulations are a necessity to achieve efficient, flexible, customised, cost-effective and high-quality production.
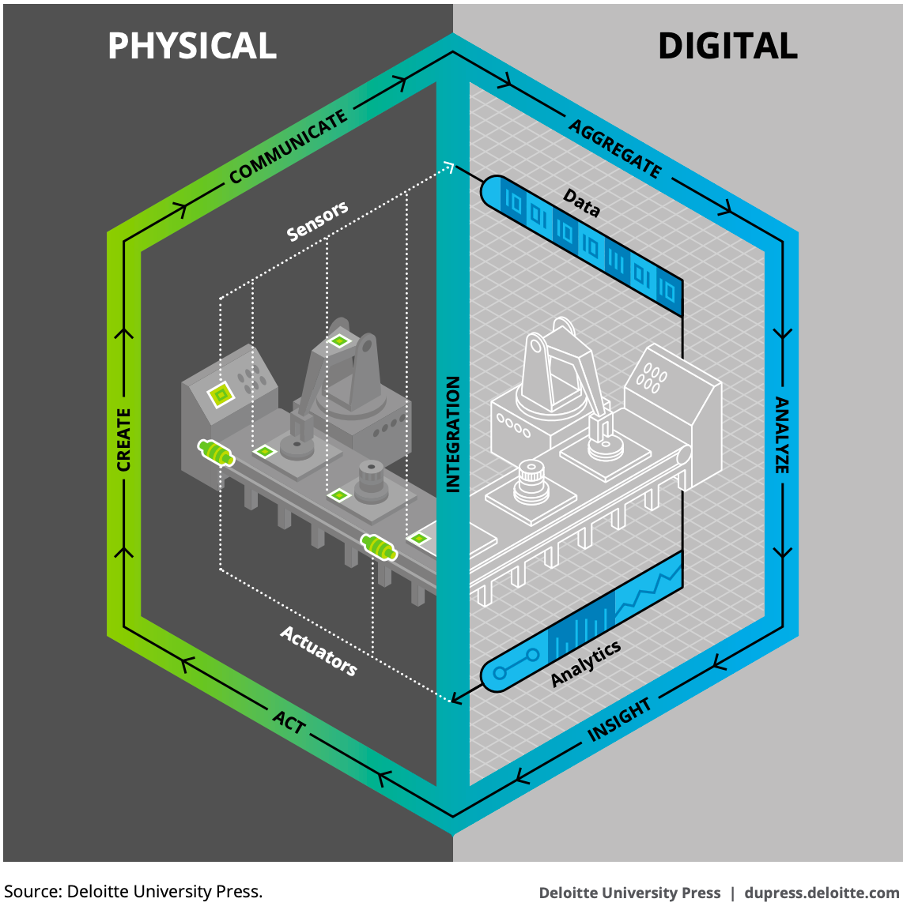
The cloud
Up to recently, most manufacturing IT systems were set up as closed in-house installations.This is now rapidly changing, as connecting globally and providing access to data has become business critical. Companies with multiple manufacturing sites are interested in centralising their data analytics to be able to learn from various locations and map across best practices. Hybrid cloud technology is helping to combine local in-house resources with the cloud, keeping production data local and enabling data analytics on the cloud.
IoT
Consumer applications have seen large scale benefits from IoT initiatives but the manufacturing industry is still finding it difficult to create solutions that are affordable, scalable and repeatable. The decreasing costs of sensors and processors are meanwhile paving the way for manufacturing to move in the direction of truly smart factories.
True efficiency in manufacturing is achieved when data can be collected at each measuring point that influences product quality, integrated between all factory systems and stored in a comprehensive data warehouse. Soon this can be done across companies, including much more than just manufacturing itself but also procurement, logistics and many more related disciplines.
Smart factory technology has been embraced for example by KUKA, who was asked byJeep to build a factory that was able to produce a car body every 77 seconds. The IoT-enabled factory houses hundreds of robots liked to a cloud system, enabling to push out over 800 vehicles a day.
Cybersecurity
Security is something that makes all manufacturers hesitant about adopting cloud technologies and often stops them from fully committing to a digital future. It is becoming clear that manufacturing companies need to quickly become knowledgeable in cybersecurity and have appropriate strategies in place. The time of keeping all production data and IP knowledge behind a physical lock and key is coming to an end.
Deloitte brings out in its Cyber Risks for Advanced Manufacturing report the different cyber threats depending on the size of company and underlines the severe shortage in talent and human capital in this area.
Augmented reality
While many of the advancements of Industry 4.0 are about automating and reducing the impact of human workers, augmented reality is all about enhancing the capabilities of human workers - giving them skills and knowledge they previously did not have. The technology offers possibilities to assist workers in the correct work sequences, show progress reports from other parts of the factory, aid in manual quality assurance, etc. The possibilities are endless and expanding as the technology is still being developed. At the moment it still requires considerable development to bring such solutions to the factory floor as the technology is in its early days.
There are several innovative ways of bringing AR to manufacturing, some of these are already in use and many more are to be introduced as the technology matures.
Conclusion
Within the last decade, the Industry 4.0 strategy has evolved to include the following four design principles:
1. Interconnectivity
2. Information transparency
3. Technical assistance
4. Decentralised decisions
Based on these principles, the future of manufacturing is likely to become more reliant on theInternet of things (IoT), AI, and ML technologies. Machines, sensors, and devices will be connected to networks where advanced ML software can optimise processes and help make decisions.
Industry 4.0 is already changing the manufacturing sector. As these technologies become more accessible, they will become the new standards for operation.